Max Scherer
Curious, hard-working, and self-motivated individual with an interest in the manufacturing and hardware of rockets and satellites.
Seeking an engineering opportunity in a space-related field in Southern California.
Background
I graduated with a Bachelors in Science and Engineering, majoring in Aerospace Engineering at the University of Michigan – Ann Arbor in May 2020. Since then, I have worked as an engineer at Northrop Grumman Corporation on a few different programs. In my first position, I coordinated and led high bay floor integration efforts of single- and multi-layer insulation for final build of the James Webb Space Telescope. In my second position, I designed and modeled a heat sink chamber and injector assembly in CATIA to facilitate testing and characterization of a potential engine design for the Human Lander System. In my third and current position, I led manufacturing and testing efforts for a 16 solar cell prototype panel with a design focused on maximizing active solar area. My various work and project experience combined with my curious and hard-working nature and my single-mindedness for problem-solving make me a strong candidate for any engineering position.
Experience
Computer Languages & Programs: CATIA, CAPE, SOLIDWORKS, MATLAB, Solumina, SPEL+, Microsoft Visual Basic, StarCCM+, AGI Systems Toolkit, C++, Java, Python, Microsoft Excel, Microsoft Access.
Work Experience: As a Solar Array Manufacturing engineer, I led manufacturing and testing efforts for Prototype 1.0, a 16 solar cell panel designed to maximize active solar area. Before I joined the program, the previous panel, Prototype 0.5-3, a 4 cell design used as a proof of concept and to qualify certain basic processes, had just completed testing. Once I arrived, one of my first tasks was to analyze the data from thermal fatigue testing of Prototype 0.5-3 solar panel and present my conclusions to senior management. Now, the manufacturing and testing of Prototype 1.0 is the number 1 priority of our program, but in between steps and when waiting for the machine shops to complete work, I have been working on process development tasks. I programmed EPSON robotic arms in SPEL+ to facilitate solder and adhesive dispensing process development and am qual-testing these new processes so that we can use them in the product in the future. When I was a Propulsion Design engineer, I designed and modeled a heat sink chamber and injector assembly in CATIA to facilitate testing and characterization of a potential engine design for the Human Lander System. Before this position, I had some experience creating and editing engineering drawings but not a ton. This position furthered my understanding of Geometric Dimensioning and Tolerancing (GD&T) and allowed me to apply it in the real world with hardware that I fully designed from the ground up. I produced both fully dimensioned and reduced dimensioned drawings in CATIA of parts for manufacturing purposes. I left the position shortly after the heat sink and injector assembly design were completed, and about two months later I got to see the completed hardware before it was sent off to testing at NASA's White Sands Test Facility. In my position as a Thermal Insulation Products engineer, I coordinated and led high bay floor integration efforts of single- and multi-layer insulation for final build of the James Webb Space Telescope, tracked the status of blanket integration and reported status daily to team and program leadership, created and revised CATIA templates and models of single- and multi-layer insulation blankets for fabrication and integration efforts, and fabricated and modified multiple insulation blankets for test and flight. My largest design project that I performed alone was the design, modeling, and fabrication of a removable contamination travel cover for the secondary mirror of JWST. After an initial prototype design and build phase, I iterated upon the design multiple times after hearing feedback from Vehicle Engineers and Contamination Control Engineers and reached a point where both parties were happy with the final cover. I worked as a Process Engineer at Moeller Aerospace for 8 months, where I modeled 3-dimensional aircraft engine components from engineering drawings in SOLIDWORKS and created operation sheets for each step in the manufacturing process, created 1:1 scale model in SOLIDWORKS of the manufacturing facilities to support rearranging the machine floor, and analyzed and generated statistics from data collected on the machine floor in order to visualize trends in non-conformities on parts. This full-time, structured co-op provided experiential learning and practical work experience in aerospace manufacturing. I was a Manufacturing intern in the machining shop floor for Aerolab, LLC, a custom wind tunnel manufacturer, and worked on a machine learning program to classify severity of macular degeneration from retina images as a Johns Hopkins University Applied Physics Laboratory ASPIRE intern.
Project Experience: My senior design project at the University of Michigan was designing, building, testing, and presenting a report for a heavy-lift quadcopter drone. I was the structures and modeling lead for the design team, taking charge of the SOLIDWORKS modeling, finite element analysis, and coordinating the manufacturing efforts of our drone. In a few short months and using only simple materials, we created a functional quadcopter with a payload capacity of approximately 10 kilograms. One of the professors in the Aerospace department was impressed with our work ethic and design and invited us to work on a project involving a VTOL, fixed wing aircraft designed to transport essential medical supplies over long distances in Ghana. Again, I was the structures and modeling lead. Unfortunately, we had just recieved the parts and begun building the aircraft when COVID canceled the remainder of the semester and we did not get to complete the build or test our design. Another design project in college was a remote controlled hovercraft that was piloted from a remote television screen and designed to pick up and deliver a payload either faster or more efficiently than other teams in the same competition. I designed and built the structural elements of the hovercraft including but not limited to a fiberglass shell, inlet and propulsion propellers and mounts, and a specially designed scoop to allow carrying multiple payloads at once.
Additional Experience: Graduated Magna Cum Laude, member of Students for the Exploration and Development of Space (SEDS) and Sigma Gamma Tau, aerospace honor society.
Why Me?
Throughout all of my work and project experience, I have gained many engineering, leadership, and organizational skills that would make me valuable to your organization. I have experience running an integration team for final build on the highbay floor of the James Webb Space Telescope and track the status of hundreds of thermal insulation blankets and running a manufacturing development lab for the R&D solar array manufacturing project I am a part of now. My time working in the Thermal Insulation Products group has taught me invaluable lessons about soft-structure, thermal insulation, 3D modeling and design, and leading a team of technicians. Working as a Propulsion Design engineer gave me a deeper understanding of GD&T and engineering drawings, both when drafting and reviewing. But more importantly than anything else, my current position as a Solar Array Manufacturing engineer taught me how to approach a new process and what is important in the early stages of a design, program, or manufaturing process. I have a wide variety of skills in computer languages and programs including CATIA and SOLIDWORKS modeling, finite element analysis, Java, Python, and MATLAB. My time as a Manufacturing Process Engineer at Moeller Aerospace is what initially introduced me to the importance of accurate 3D modeling and Geometric Dimensioning and Tolerancing (GD&T), which I used daily to represent the precision aircraft engine components manufactured on the machine floor in the next building over. In addition, the summer after my freshman year I interned in the metal shop for a custom wind tunnel manufacturer, Aerolab LLC in Jessup, Maryland. This experience was essential to growing my understanding of manufacturing and engineering design as well as developing my communication and collaboration skills. As an intern in the shop, I learned how to operate various machinery including a lathe, drill press, and bandsaw. I also gained valuable experience in the physical restrictions on designs while I was there, seeing multiple times where the computer drafted schematics were near impossible to physically create and the senior machinists had to adjust or redesign parts to complete the wind tunnels. Through all of my experiences I used my focus and abilities to creatively problem solve in order to complete the required work. I am ready and excited to apply my knowledge and skills in my next position.
Contact
email me at my personal email maxwellhscherer@gmail.com
call me at 410.979.7436
I currently reside in Long Beach, CA 90802
click this to go to my linkedin
or, click this to download my resume
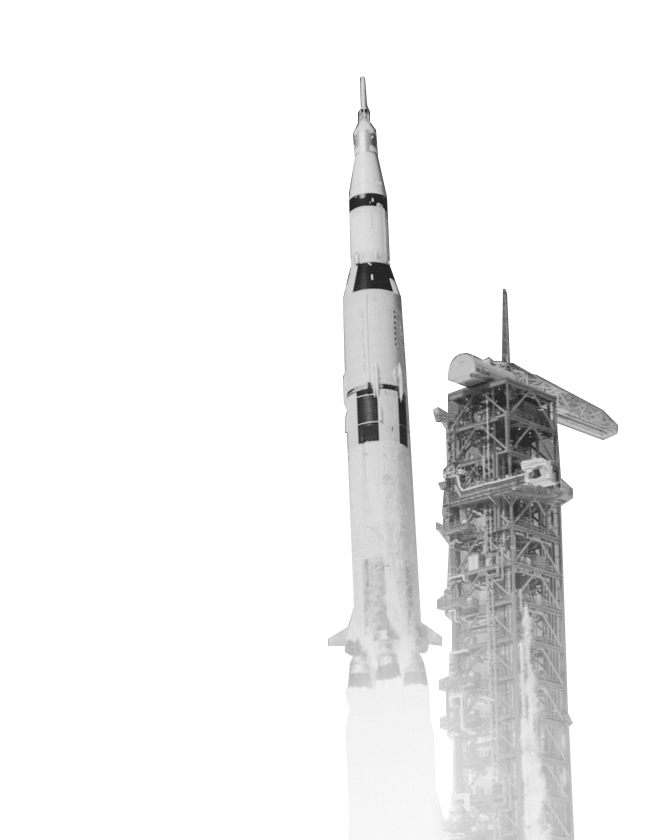